U.S. Cold Storage Warehouse Inventory
Consumer preferences for fresh and frozen foods, online shopping and use of biologic and biosimilar pharmaceuticals is fueling investment in the cold storage warehouse industryNorth American, especially U.S. cold storage warehouse space is currently at a premium. According to industry experts, the average occupancy across the U.S. cold storage warehouse industry is 85%, considered full occupancy. Due to increased meat supply and trade disputes, 2.5 billion pounds of meat is stockpiled in American refrigerated warehouses across the country. U.S. refrigerated warehouses are at or near capacity. While expected to be temporary, the challenge of dealing with a cold storage warehouse industry that is near capacity has become commonplace.
Recently there has been declining availability of cold storage warehouse space. Add to this a narrowing gap between delivery of new refrigerated warehouse space and absorption of existing space and it is understandable by construction of cold storage warehouses is again picking up steam. Rising labor and construction costs coupled with the needed infrastructure and technology needed for daily operations means that cold storage warehouses are more expensive to build than ambient warehouses.
Industry projections reveal that global demand for fresh and perishable goods will continue to drive demand for cold storage warehousing for the foreseeable future and the online grocery shopping is continually increasing.
Sale-leaseback arrangements have become popular in the refrigerated warehouse industry. Here is how this works: the warehouse owner-operator sells a warehouse then immediately signs a long-term lease on the property, enabling them to improve cash position. This arrangement is favored as it allows warehouse operators to manage their facilities while enabling investors to earn cash flow from rent payments.
Increased obsolescence of older facilities is a significant issue facing the cold storage warehouse industry today. Nearly 48% of all active refrigerated American warehouse facilities were built prior to 1980, the advent of automated cold storage warehouses. Starting in the 1980s, cold storage warehouses began utilizing automated cranes to enable warehouse workers to stack goods at increasing heights. Capable of reaching higher shelves and navigating narrower aisles, the use of automated cranes has enabled cold storage warehouses to achieve up to three times greater efficiency as compared to operations using manual forklifts. Since the adoption of automated cranes, the average ceiling height of a cold storage warehouse has increased from 23 feet in 1980 to 38 feet in 2010.
Escalating land prices and capacity restraints have consequentially resulted in a need for more vertical development, increasing ceiling heights to provide more warehouse storage capacity. In the refrigerated warehouse industry, the issue of energy cost and conservation is compelling. Taller buildings tend to be more energy efficient as compared to lower and wider buildings of comparable volume due to the tendency of heat infiltration to occur through the roof and floor. Another reason for the construction of taller cold storage warehouses is their ability to utilize automation.
What Factors Are Fueling the Need to Build More Cold Storage Warehouses?
Factors impacting the need for more refrigerated warehouses
Increased Population=Increased Need for More Cold Storage Warehouse Space
From grocery to foodservice, meal kits and temperature-sensitive pharmaceuticals, the need for refrigerated warehouse space expands with a growing population. Due to the potential for foodborne illness and spoilage, perishable food and pharmaceutical products require proper handling and storage and may require temperature monitoring to ensure quality.
Increased Demand for Protein
With incomes rising across the world, the explosion of new consumers has fueled an appetite for protein. Whether valued as an out-of-reach commodity or treat or a symbol of rising incomes, meat is popular. In 2018, the average American consumer is anticipated to eat an average of 222.2 pounds of red meat and poultry this year.
Need to Move Refrigerated Warehouses Closer to Consumers
With the increase in online grocery ordering, restaurant delivery and meal kits, perishable food goods need to be stored much closer to consumers to ensure speed of delivery.
Food Product SKU Proliferation
Today consumer purchasing patterns have demonstrated increased preference for a wide variety of goods including ethnically diverse food products and a rising trend towards the segmentation of fresh foods based on classifications including gluten-free, vegan, organic, non-GMO, etc. Consumer food preferences have changed substantially and this is necessitating changes in the food supply chain. The sections of the supermarket that are thriving are those devoted to refrigerated and frozen foods.
E-Commerce and Online Shopping for Grocery Items
Increasingly, consumers are ordering more food products to be delivered to their homes. Consumers crave convenience. Increased consumer demand for home delivery of meals, meal kits and perishable grocery goods is transforming the cold chain. The home grocery delivery and meal subscription service sectors have been picking up steam over the past few years. Supermarkets have demonstrated intense interest to invade the meal kit space, as it seems to provide a potential competitive advantage.
Jump in Use of Temperature-Controlled Pharmaceuticals Increases Need for Cold Storage Warehouses
According to Pharmaceutical Commerce’s annual Cold Chain Sourcebook for 2017, temperature-controlled products are growing at more than double the rate of non-temperature controlled products.. According to In a 2017 survey of 140 temperature-controlled logistics professionals surveyed, 20% were actively working on enhancing their network of cold storage facilities within the next 12 months.
New popular medications, primarily biologic and biosimilar pharmaceuticals often are temperature-sensitive. In fact, 23 of the 57 newly approved drugs in 2017 require standard refrigeration of between 35 and 46 degrees Fahrenheit during storage and transport. Vaccines, biotechnology products and products using living cells are susceptible to damage from freezing and excessive heat. This results in product loss of therapeutic and financial value.
In addition, commercial blood products, stem-cell products, cord-blood bank, tissue and organ products as well as products used in clinical trials require temperature-controlled logistics and storage.
Year-Round Fresh Produce
Okay, we admit it. As consumers, we have become quite spoiled. From watching famous chefs cook up gourmet recipes and off-season feasts, it all seems so easy. We must be able to find the necessary ingredients. From watermelon in a North Dakota supermarket in the dead of winter to pumpkins in the spring, American consumers are willing to pay for off-season fresh produce if it tickles their taste buds. This means that many fresh fruit and vegetable products are imported and travel long distances to reach the salad bowls of American consumers. Highly susceptible to damage, fresh produce requires refrigerated transport and storage conditions.
Shift to Eastern U.S. Ports
With the recent expansion of the Panama Canal and rise of modern and more efficient Eastern seaboard ports, ports along the West Coast of North America have found the competition fierce. Eastern U.S. ports by comparison have led port modernization efforts and tend to be more likely to have robotic cranes as well as better on-dock rail services to the ports.
Conclusion
Whether you are a food processor, distributor, retailer or distributor of perishable food products, a cold storage warehouse is essential to your business. Cold storage and logistics providers make use of every bit of cubic feet in the warehouse, whether for frozen foods or pharmaceuticals.
The future is bright across the supply chain for technologies and warehouses and distribution centers used for food and pharmaceutical products. Refrigerated warehouses rely on specialized technology to ensure quality control and product safety, provide inventory control and inventory management functionality and handle order fulfillment. In comparison with dry warehouses, cold storage warehouses tend to be more expensive to build. Specific technologies are often used in cold storage warehousing to manage temperature zones, minimize heat loss and monitor each product being stored.
Some of the factors leading to the construction of new cold storage warehouses include increase in online grocery shopping, adoption of biologic and biosimilar pharmaceutical products and widespread consumer preference for fresh, perishable and frozen foods.
What Makes Datex Different?
1. Revolutionary low code/no code flexible workflow-driven warehouse management software
2. Most configurable, user-friendly WMS on the market today
3. End-to-end solution provider: software, hardware, EDI, and managed services
4. White Glove Concierge Service
5. Executive-level attention and oversight
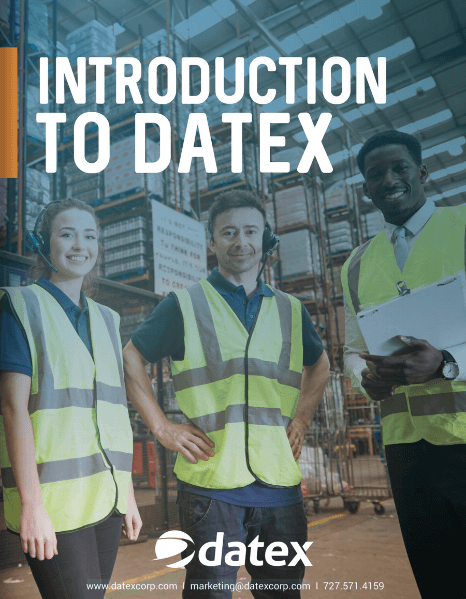