The COVID-19 Effect: Supply Chain Shortages and Rising Prices
Supply Chains Disrupted by COVID Still in Flux
When one stops to think about the complexity of today’s supply chains, disruption almost seems inevitable. Supply chain disruption and product shortages seem to be the hot topic of the day. From the sourcing and procurement of raw materials and components required to manufacture goods to the distribution, warehousing, transportation, and logistics of products to the end customer, many things can go awry. Today, supply chains extend around the world. This can mean that raw materials are procured from one country, transported to a second country to produce a component which is then assembled into a final product in a third country. The finished goods may then be transported to multiple countries where they are warehoused until distribution to the end customer.
Yes, the world has seen natural disasters previously, however none has impacted the entire world’s population as COVID-19 has. Typically, a natural disaster disrupts some industries while others remain unscathed. COVID-19 seemed to touch all markets and industries and the impacts are still being felt today. Natural disasters often effect global supply chains but are short lived. Experts estimate that the impact of COVID-19 on global supply chains and economies will still be felt for at least a decade, if not longer. The sheer scope of the coronavirus’ impact is simply staggering.
COVID was like a bad break up to a relationship. Getting over it simply takes time.
Take, for instance, the manufacturing industry. For many years, numerous industries have operated successfully using a just-in-time (JIT) strategy. While not especially flexible, the strategy proved effective in keeping costs under control and maintaining operational discipline. The JIT strategy dictates that goods are produced right before they are needed to prevent the need to store massive amounts of inventory.
JIT is common in the auto industry, for example. A shortage of labor, raw materials or components can force manufacturers to shutter operations temporarily. Today, across the world, businesses are dealing with a semiconductor shortage that has its roots in the COVID pandemic. The shortage of semiconductors is so acute that it is not expected to alleviate until some time in 2022. Some auto plants have been forced to close until the needed parts arrive. In the short term, workers are unable to work and cars are not rolling off the production line. With stimulus checks heading to homes where anxious consumers are ready to venture out and spend money, will the lack of inventory affect the economy?
Manufacturers appear to be charting a new course. According to a 2020 survey conducted by law firm Foley & Lardner LLP, 62% of the manufacturing executives surveyed noted that they have decreased focus on just-in-time inventory models. 70% of those surveyed indicated a change in focus away from sourcing from the lowest cost suppliers to instead concentrate on supply chain resiliency.
Some of the Top Issues Plaguing Supply Chains
- Changes in Consumer Demand in Both Volume and Variety of Manufactured Goods
- More Direct-to-Consumer Transactions and Online Ordering
- Pent-up Consumer Demand (from COVID-19 restrictions limiting store and shopping access)
- Shake Up of Transportation Networks Handling Logistics of DTC Orders
- Workforce Availability and Location
- Launch of Food Protectionist Policies by Country Due to COVID-19
- Shortages of Raw Materials and Component Inventory Slowdown Production
- Increased U.S. Household Savings Rate (18 percent during pandemic versus typical 7 percent annually)
- Trends Causing a Spike in the Popularity of Specific Products
ISSUE SPOTLIGHT
Labor Shortages and Workforce Challenges
American manufacturers employ approximately 13 million workers. Because of the nature of the work they do, manufacturing workers must work in production facilities and cannot take advantage of the trend to working remotely. They have been subject to the risk of contracting COVID and had to deal with changing working conditions designed to help mitigate the risk of becoming infected with the coronavirus.
At the height of the pandemic, manufacturers in many industries struggled to produce goods while still protecting workers so that COVID-19 did not spread. Frustrating and expensive for manufacturers, the added stress put more pressure on workers. This is one of the reasons, along with a shortage of labor to work in various sectors of supply chain operations that companies have been evaluating use of automation technologies.
Did you know that today the U.S. is producing approximately the same amount of goods and services it produced before the 2020 COVID-19 pandemic but with 8.2 million fewer workers?
One thing that businesses learned from the coronavirus lockdown was how to do more with less labor. From artificial intelligence, machine learning, robotics and drones to material handling solutions, the crisis forced supply chain businesses to leverage technologies and find new ways to increase workforce productivity. Leveraging automated technologies also helps to keep human workers safe while ensuring the continued productivity of the facility.
ISSUE SPOTLIGHT
Shipping Container Crisis and Port Congestion
It is important to note that during the coronavirus pandemic, trade continued to flow. Although presidential proclamations were issued in March 2020 which restricted travel from numerous countries, the ports remained open and goods continued to flow across borders.
Are shipping containers endangered? No, probably not, although some ports have an abundance while others have nearly none.
Approximately 170 million shipping containers are used to transport 90% of the world’s goods across the world. As the world’s foremost manufacturing center, most of the goods flow outward (export) from Asia, specifically from China, home of seven of the largest container ports globally. When countries around the world were locked down, goods did not ship out of China for two months. North America and Europe were shut down as China recovered and began to reopen its economy.
During this period, however, consumers were unable to spend money on travel and other services. Trapped in their homes with their families, consumers spent money online on medical goods, protective gear, consumer packaged goods, as well as home furnishings and electronics to make their homes more serviceable and comfortable for their families.
As demand for commodities including computer equipment, medical equipment and home office goods soared last summer, the United States imported many of these goods and materials from China. Months of suspended trade caused an imbalance. Nearly three containers of goods were exported for every one container that was imported.
Chicken Shortage
You may have noticed that the supply of chicken seems to have dwindled over the past year. It is not your imagination. A shortage of chicken wings just in time for picnic season? Say it ain’t so! During last year’s pandemic, meat packing facilities were challenged by the need to adapt operations to keep workers safe. Production dropped. Chickens were culled. The volume of chicken produced for sale this year is down.
Tyson noted another specific problem to their business. The company had selected a different variety of rooster as the characteristics of this type of rooster improved its offspring chicken’s quality for meat. Unfortunately, this variety of rooster produces fewer eggs and is known for having lower hatch rates than the type of rooster previously used.
The war over chicken sandwiches is still raging. The popularity of Popeye’s fried chicken sandwich to new versions at Kentucky Fried Chicken, McDonalds and other fast casual restaurants is also tied to the chicken shortage.
In addition to the other challenges, Tyson also lost a week of production due to a devastating February winter storm in Texas which crippled their entire poultry enterprise.
Plastics shortage
The plastics shortage has been in the works for quite some time. Not only did 2020 see the advent of the pandemic but also a hurricane which wrought significant force and damage upon the petrochemical industry. In August 2020, Hurricane Laura came ashore on the Gulf Coast, forcing the closure of petrochemical factories in Texas and Louisiana. This single storm shut down 10-15 percent of the production of essential chemicals needed to make plastics.
Next, big polymer producers including LyondellBasell in Louisiana and Chevron Phillips Chemical in Texas declared force majeure. The force majeure clause commonly found in contracts, when executed relieves companies of specific supply-delivery commitments due to circumstances that are beyond their control.
The COVID-19 pandemic impacted the industry in another way. Many workplaces implemented safety protocols to help keep workers save. The changes often slowed down production and caused labor and trucking shortages at ports.
If that was not enough to wreak havoc on the plastics industry, the February 2021 winter storm which impacted the Gulf Coast of Texas had a significant impact. Texas is the hub for petrochemicals, used to turn oil and gas and other byproducts into plastics.
Given the fact that approximately 100 essential chemicals and derivatives that are widely used to make products for various industries are processed in Texas, experts estimate that it will take a minimum of six months to recover from the imbalances caused by the storm.
With the anticipated surge in demand as consumers begin to venture out and spend their stimulus checks, supply-demand imbalances are expected to worsen.
“Shifting Bottlenecks” in Supply Chains
Supply chains are multi-tiered and operate in numerous stages. For example, to make goods, the raw materials and components required for production must first be sourced, procured and transported to the right location at the right time. Labor shortages, lockdowns, union disputes, etc. can directly impact these processes, delaying part or the entirety of production and impacting lead time. Once this occurs, often a chain reaction of delays and bottlenecks begins.
The cold chain is more complex and variable. To protect the safety and viability of perishable goods, each aspect of the supply chain needs to be monitored. The task of monitoring, transporting, and storing these fragile goods is further complicated by the temperature requirements of each product, whether products must be cooled, frozen, even stored in ultra-cold temperature conditions. When there is a delay in the cold chain, the level of complexity tends to cause problems to multiply exponentially. This is often because cold chains have a series of sequential steps in their operations. The potential for problems at every step of each process mean that there is a greater likelihood that the temperature requirements have not been met or maintained.
With the advent of COVID-19, cold chain operations were challenged beyond expectations. With workforce shortages, the huge surge in demand and numerous other factors, food distributors and processing centers found it taxing to keep up the accelerated pace.
Although demand has, for the most part, normalized, challenges still loom. No one knows what lingering effects may prevail to change the supply chain landscape, possibly for good. Foodservice and restaurants suffered as demand took a nose-dive. Food and beverage processors and distributors suddenly were expected to make adjustments on extremely short notice to meet customer demand.
2020: Lessons Learned
1. Visibility is critical.
Partner with technology vendors, suppliers, customers and others in your supply chain to ensure that everyone works from the universal truths of your piece of the market. Data collaboration can help shore up blind spots and facilitate better working relationships, understanding of trends and ways your supply chain can function better to meet demand.
2. Leverage technology.
Whether your business suffered from a shortage of labor or a temporary adjustment to accommodate the safety needs of workers, using technologies can help maximize the impact of the labor you have, making it more effective. It can also augment your workforce and help your company remain in operation, even if human workers must be sent home.
Conclusion
From the toilet paper shortage redux to lumber prices surging, the economy is recovering like a runaway car on a roller coaster. As Bette Davis admonished in the classic 1950 film “All About Eve”, “fasten your seatbelts, it’s going to be a bumpy ride”.
The global economy is going to take awhile to adjust and come to a new level of balance. While the digital transformation of the supply chain would provide needed visibility, it is still a work in process, a distance away.
Many companies are now focusing on resiliency and flexibility. With advanced supply chain planning and operations management practices focused on keeping costs under control while still providing for multiple options, companies are gaining more control over their businesses in these dynamic times.
From the United Kingdom to the Middle East, global supply chains are trying to stabilize. Labor shortages, material shortages-it seems as if new shortages are popping up every day. As the COVID19 pandemic wanes, supply chain management has made advances using technology to mitigate supply chain disruptions and risk. Perhaps soon, we can shift from getting daily guidance from the Centers for Disease Control and instead concentrate on global trade and supply chains.
At the end of the day, perhaps the best advice is patience and a strong seatbelt.
What Makes Datex Different?
1. Revolutionary low code/no code flexible workflow-driven warehouse management software
2. Most configurable, user-friendly WMS on the market today
3. End-to-end solution provider: software, hardware, EDI, and managed services
4. White Glove Concierge Service
5. Executive-level attention and oversight
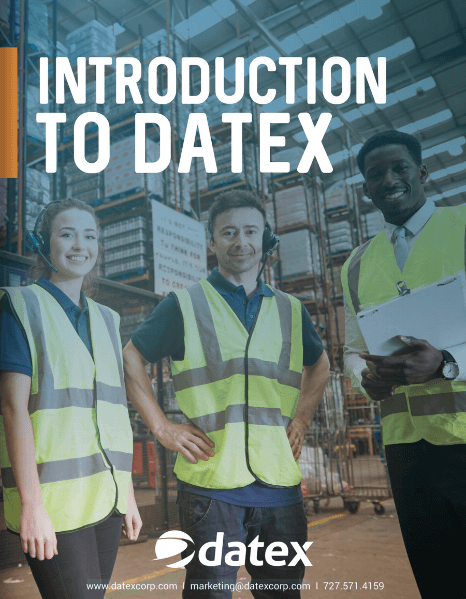
Industry Specific WMS
Resources
Shortages are popping up across the supply chain as the pandemic messes with the economy – CNN
Chickens are in short supply. Blame Tyson’s roosters – CNN
Supply chain price increases: Gas, homes, lumber and chicken are all increasing – CNN
Keeping Trade Flowing | U.S. Customs and Border Protection (cbp.gov)
The Latest Supply Chain Disruption: Plastics (hbr.org)
Still out of gas, and other shortages costing America (msn.com)
Made on Earth: Global trade defined in eight everyday items (bbc.com)
https://www.foodengineeringmag.com/articles/99366-big-things-to-know-about-supply-chains
How has COVID-19 impacted supply chains around the world? | Hub (jhu.edu)
How The Shipping Container Crisis Demonstrates The Risk Of Imbalance In Global Trade (forbes.com)