Supply Chain Labor Shortages and Technology
Labor Shortages across the Supply Chain Can Be Mitigated with TechnologyStrong consumer, anticipated increases in consumer spending and the dynamic labor market have proven challenging this year. As the economic recovery continues and the COVID19 pandemic drags on, the holiday season is approaching fast and with it, concerns about how the supply chain can overcome these debacles.
Labor Shortages, Supply Chain Woes
Manufacturing Workforce
Across the supply chain, labor shortages abound. The manufacturing worker labor shortage, both in terms of unfilled jobs and the manufacturing skills gap is anticipated to cost the United States as much as $1 trillion in 2030 alone by leaving 2.1 million jobs unfilled. According to the National Association of Manufacturers (NAM) Manufacturers’ Outlook Survey, finding, training, and retaining talent are among the primary challenges plaguing the industry.
During 2020, the manufacturing industry netted a loss of 578,000 jobs. Surprisingly enough, at any given time within the past six months, up to 500,000 manufacturing jobs have remained unfilled. Why?
There remains a significant skills gap in American manufacturing. As an industry, manufacturing has traditionally been viewed as essential, but not attractive to younger workers. As Baby Boomers leave the workforce, there are not enough younger workers entering the manufacturing industry to compensate and fill the gap. The workers leaving the industry tend to be relatively highly experienced and skilled. Younger workers find the lack of prestige involved in working in a factory unappealing.
Innovative technologies have been introduced to the manufacturing industry, including robotics, automation, artificial intelligence (AI), and machine learning, and are becoming increasingly popular in use. The manufacturing industry is becoming more technical in nature, requiring more than simply uneducated and unskilled workers to do manual labor in sometimes uncomfortable surroundings.
Today, manufacturing workers need to be able to embrace technology. This new generation of factory workers needs to develop the skills to operate and program advanced technologies, including robots and automated systems as well as work with humans. Technicians on a variety of skill levels are key, and high-paying jobs are available, but remain unfilled.
Truck Drivers
The American Trucking Association reports a current shortage of 63,000 truck drivers and anticipates a shortage of 175,000 truck drivers by 2026.
- Aging workforce. The average age of a truck driver is 55 years old. During the pandemic, many drivers retired early or decided to leave the trucking industry due to concerns involving COVID-19.
- Lifestyle concerns. Many workers find it difficult, especially for long haul trucking, to sustain interpersonal and family relationships in this profession.
- Frustrating working conditions. Long hours, poor road conditions including traffic, accidents and detours plus little interpersonal contact make many workers dissatisfied with their profession.
- Truck drivers frequently report frustration that too much of their work is unpaid, leading to dissatisfaction with their salaries. This is especially true of veteran drivers with more than five years of experience. Compensation is a matter of increasing concern, especially since the advent of the electronic logging device (ELD) mandate. When a truck driver is delayed, no matter the reason during the permissible driving time, he or she loses miles and compensation.
- Industry culture. The trucking industry has a perceived culture of long hours, low pay, little respect, and undesirable working conditions. This is especially unattractive to younger workers potentially interested in entering the transportation and logistics industry.
- Fear of the future. As autonomous vehicles, including driverless trucks have been developed and are being tested, this has increased the anxiety of truck drivers for their future in the transportation industry.
Warehouse Workers
The unforeseen escalation in the popularity of e-commerce orders arrived at a time when the warehousing industry was already plagued by a shortage of warehouse workers. The transportation and logistics industry has struggled for years to attract, train, and retain workers as the workforce ages out and the gap remains unfilled.
Also viewed by many job seekers as undesirable work, working in a warehouse is typically manually oriented, physically demanding work. As e-commerce gained popularity, the sheer number of individual orders rapidly escalated. No longer were warehouse workers mainly moving goods by the pallet. Now order pickers have to pick orders by the piece, not by the pallet. This is time consuming work often involving significant travel time, walking from place-to-place.
The Complexity of 3PL Operations Magnifies Labor Shortage Complexities
In the 2021 Inbound Logistics Perspectives: 3PL Market Research Report published in July, 47 percent of shippers and 73 percent of 3PLs report that finding, training and retaining qualified labor is one of their top challenges.
Third party logistics providers face major supply chain challenges. Managing inventory for multiple clients, each with its own labels, invoices, reports, operational processes, billing, and other unique elements, 3PL operations tend to be more complex.
Technology Enables Labor Productivity
Warehouse Automation
Years ago, warehouse automation was considered innovation, affordable for e-commerce enterprises but not widely used. Today, robotics and other forms of automation systems are becoming more popular, partially because of labor shortages as well as driven by the need for high speed and accurate e-commerce order fulfillment.
For example, as e-commerce orders boomed in popularity, goods-to-person automation systems started to become more readily adopted. The use of goods-to-person systems reduces the time of walking around the warehouse, picking goods. Order pickers have been estimated to spend 70-75% of their time traveling from place-to-place picking inventory for orders. The adoption of goods-to-person and other automated solutions can double or even triple productivity.
Types of Warehouse Automation and Their Respective Benefits
- Pick-to-light systems (light-enabled solutions)
- Provides nearly 100% accuracy
- Facilitates faster picking as compared to traditional pick methods
- Easy to use, making it easy to learn and use
- Integrates readily with material handling solutions
- Voice technologies: voice picking, voice tasking
- Boosts order accuracy
- Quick to set up
- Easy to learn, use and adopt, reducing training time
- Reduces picking errors
- Goods-to-person systems, involving use of robots or machines which transport materials to workers for packing or assembly
- Significant increase in efficiency
- Eliminates warehouse worker travel time
- Boosts labor productivity
- Increased accuracy
- Sortation systems
- Reduces travel time of labor resources
- Decreases labor costs
- Streamlines packing operations
- Expedites order processing
- Co-bots, also known as collaborative mobile robots (human worker works alongside robot)
- Easy to program and set up
- Flexibility, can be used in multiple departments
- Improved consistency and accuracy rates as compared to human workers
- Helps boost productivity and process optimization
- Automated Storage and Retrieval System (AS/RS)
- Helps warehouses maximize floor space, boost storage capacity, optimize vertical space
- Helps reduce the time warehouse workers walk the floor searching for inventory
- Helps expedite picking and packing processes
- Enhances inventory control
- Enables human labor resources to focus on higher level, less repetitive tasks
Warehouse Management Software
Today, most warehouses rely on warehouse management software. Although some systems are easy to navigate, others may be cumbersome to learn and use, making training time excessive. With the high rate of turnover in most warehouses, this can be problematic. When warehouse workers become frustrated with technology, it is common for them to skip steps, instead substituting manual operations or shortcutting processes. This can lead to inaccurate data, lower order fulfillment rates, inventory damage and diminished workforce productivity.
User Friendly WMS
Having the right technology can make quite a difference in warehouse operations. For example, having a user-friendly WMS user interface can help to make the software easier to learn and use, improving user adoption rates. Warehouses are notorious for having high turnover rates. Think about it. Every time a warehouse worker leaves, and another takes his or her place, the worker must be trained to use the WMS. If the software is cumbersome and not intuitive, it can frustrate users and slow down the learning process. This is especially problematic for warehousing companies during the holiday season when temporary workers are hired.
Training
Does the WMS software developer provide comprehensive training, including an online component? Warehousing companies can benefit significantly by being provided with a variety of training methods, including in person, online training and demonstrations, virtual learning systems, software demonstrations on a step-by-step basis and other methods. Every person is different. Some people learn by watching demonstrations and videos, others need to read training materials and manuals or receive in person instruction, with the opportunity to ask questions directly by the trainer.
Having multiple training methods and updated training information is updated is of vital importance. These days, warehouse operations are undergoing tremendous change, altering processes, adding new technologies which can alter operational processes. Without training, warehouse workers are forced to rely on tribal knowledge which tends to be less accurate. This facilitates the development of bad habits, manual processes, and workarounds by the workforce, decreasing the productivity of the labor resources.
Features to Boost Workforce Productivity
Having at least some basic labor management functionality can enable warehousing companies to exert greater control over the level of productivity of the workforce. Having labor management functionality can help warehousing companies to better identify productivity gaps and manage unproductive work time. In addition, labor management functionality can aid in identifying underperforming workers or shifts.
Here are some of the labor management features that can be helpful for warehouses to make sure are included in a warehouse management system:
- Task Interleaving
- Labor resource allocation, tracking and monitoring
- Real time workforce visibility, by resource
- Labor forecasting
- Workforce scheduling and planning
- Ability to manage the workforce from a single screen
- Workflow-driven task assignment to workers
- Configurable reporting and dashboards with drill down detail
Driverless Trucks
According to transportation logistics industry researchers, driverless trucks may replace truck drivers as early as 2027, eliminating 1.7 million American truck driving jobs. In the United States, there are 3.5 million professional truck drivers. In its entirety, the trucking industry employs 8.7 million people.
A form of driverless trucks, autonomous technology is widely used in the mining industry. Autonomous haulage systems (AHS) are increasing in popularity and are used to enhance the efficiency, maintenance, and safety of mining operations. The use of AHS helps to reduce the risk of injuries at mine sites, reduces fuel consumption and emissions.
Autonomous trucks rely on sensors, including lidar, radar and cameras to gather and disseminate data to a computer which controls the truck. The autonomous truck learns a variety of skills through a tremendous amount of simulation and training. Sensors are often mounted higher off the ground, providing better visibility because of the height and dimensions of a truck as compared to that of a car. Because long haul truckers typically follow fixed routes and travel largely via highways, launching autonomous trucks is theoretically easier than that of launching autonomous private vehicles.
Autonomous trucks must be able to sense road and travel conditions farther in advance to enable the longer stopping distance. Some manufacturers leverage multiple HD cameras looking up to 1,000 meters ahead to detect other vehicles on the road, provide information to calculate their trajectories at that distance. This is normally twice the distance that professional truck drivers can view while driving.
Conclusion
One can apply the proper principles of supply chain management, operations management, monitor supply and demand and go to Harvard Business School, but having a labor shortage can still result in supply chain disruptions. From social media to mainstream media, the word is out. There are plenty of job openings across the supply chain as the economic recovery continues to move forward from the COVID19 pandemic. The labor market is awash with opportunities in manufacturing, warehousing, and trucking yet labor shortages continue, resulting in supply chain issues.
Because the warehousing industry is challenged by slim profit margins, warehouse operators are often opposed to raising wages significantly, however that is starting to happen across the country, at least somewhat. In April 2021, Amazon made the news by announcing it would raise the wages of more than 500,000 of its fulfillment center workers somewhere between 50 cents and $3 per hour beginning in May.
In today’s world in which the top stories involve major players battling for prime industrial real estate space, optimizing the customer experience, and facilitating global trade, one cannot forget the basics. Having enough truck drivers, warehouse workers and a skilled, experienced manufacturing workforce is the backbone to the supply chain in North America. From the White House to Big Box boards of directors, it seems like supply chain businesses across the country are looking for solutions to either resolve the labor shortage or find ways to leverage technology to augment, supplement or replace human workers.
Relying on tried-and-true technologies such as warehouse management systems as well as new technologies including artificial intelligence and machine learning, supply chain businesses across the country are trying a variety of tools to supplement, support or replace labor resources for better performance.
What Makes Datex Different?
1. Revolutionary low code/no code flexible workflow-driven warehouse management software
2. Most configurable, user-friendly WMS on the market today
3. End-to-end solution provider: software, hardware, EDI, and managed services
4. White Glove Concierge Service
5. Executive-level attention and oversight
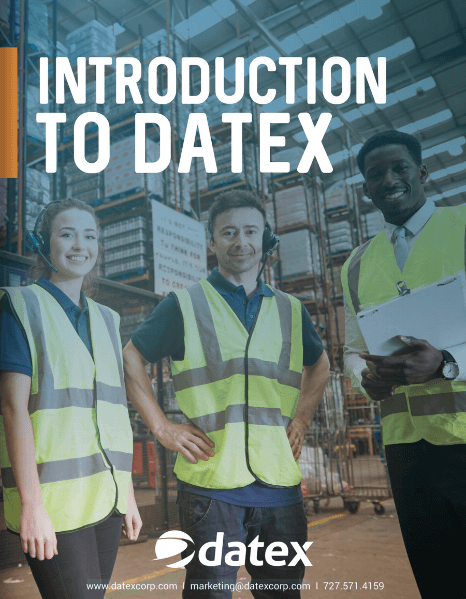
Industry Specific WMS
Resources
https://www.smart-trucking.com/truck-driver-shortage/
https://doft.com/blog/when-will-automation-take-over-trucking-industry-scientists-now-have-estimate
https://www.mining-technology.com/mining-safety/autonomous-haulage-systems/
https://spectrum.ieee.org/this-year-autonomous-trucks-will-take-to-the-road-with-no-one-on-board
The Future of Warehouse Work: Technological Change in the U.S. Logistics Industry (berkeley.edu)
The Warehouse Labor Gap is Unsustainable – Logistics Viewpoints