Tip #25: Dock Door Appointments Reduce Interruptions
Provide an accurate, efficient system to record arrival and departure times. Make your warehouse “driver friendly” by installing a system that shows the updated dock door schedule with color coded status. This will make it less frustrating and user friendly for drivers to understand while waiting. Using a status-based color coded system will help to minimize questions and interruptions, making your team more productive.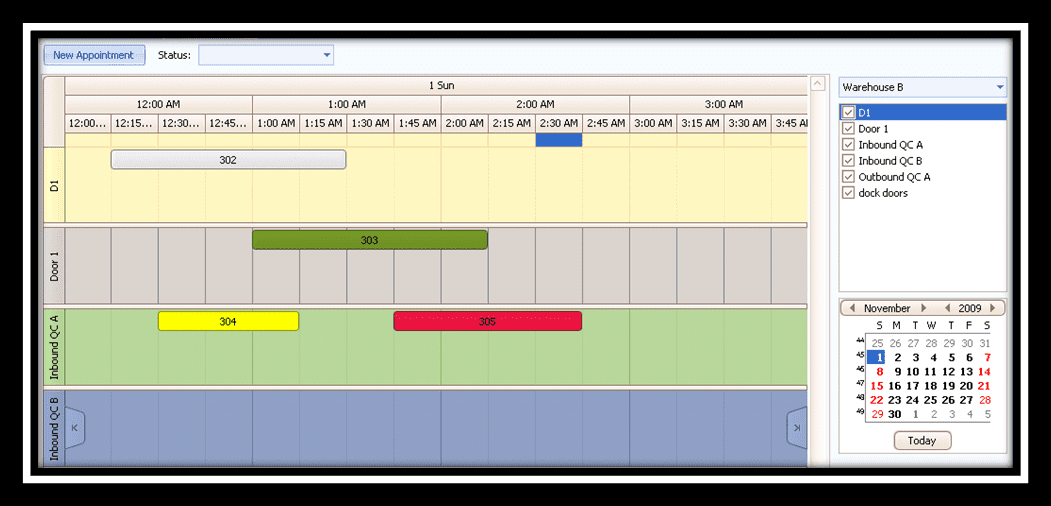
Tip #26: Training Can Help Reduce Damages and Worker Injuries
Properly educating warehouse workers who handle receiving and delivery will pay off in the long run. Make sure you train workers on how to use box cutters so that they can avoid scratches, rips, injury and costly product damage. Each box should have opening instructions shown on the outside specifying where to and not to cut in order to protect merchandise inside the package.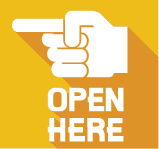
Tip #27: A Place for Everything and Plenty of Space for Forklifts
To prevent damages and reduce frustration and wasted time, make sure that crossdocks and warehouses have uncluttered, easy to maneuver aisles for forklift movement. Make sure that you consider various types of handling equipment when positioning inventory. Some types of product loads can be damaged if handled by the wrong kind of equipment. Training your workforce as to proper equipment use can help to reduce injuries and damaged products.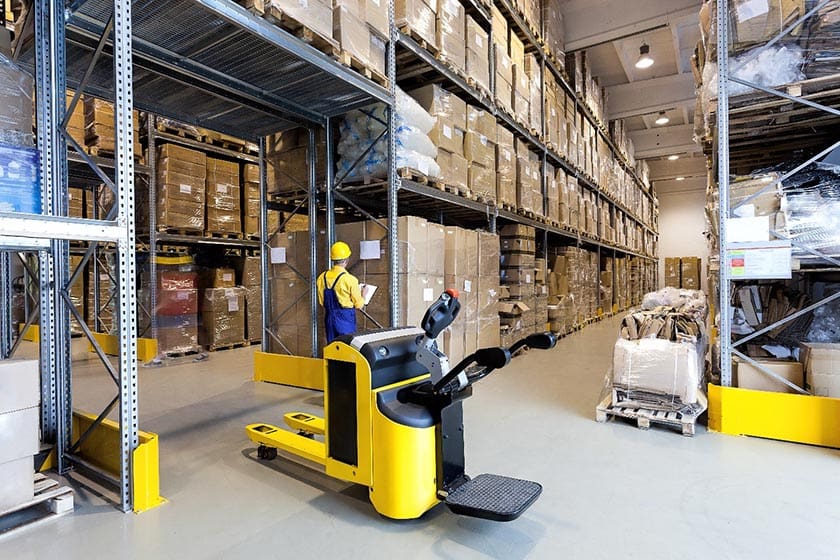
Tip #28: Use a Dimensioning System to Reduce Shipping Costs & Labor
Measuring parcel dimensions manually takes more time and is subject to error as compared to simply weighing a package on a conventional postal or shipping scale.
Need to speed up warehouse shipment processing and eliminate costly errors as well as the labor associated? Try implementing a dimensioning system in your warehouse. Sensing and imaging technology is used in order to calculate package dimensions to determine dim weight.
Using a dimensioning system can maximize your shipping process flow and reduce costly labor. Some dimensioning systems can integrate with shipping software and scales to provide package weight and dimensions at the same time.
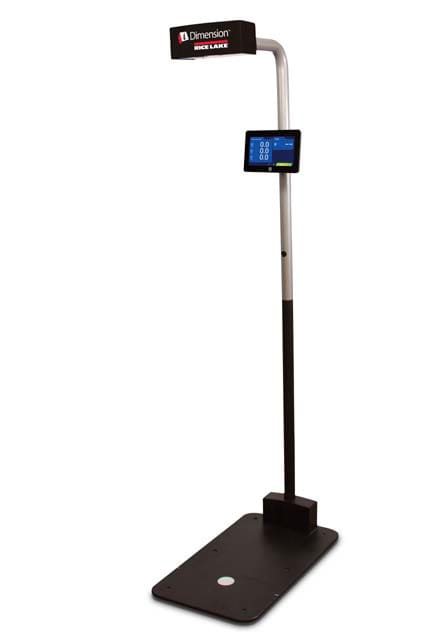
Tip #29: Advance Notice Keeps Your Operation at the Ready
If you are one of the many operations that still has not implemented advanced shipping notifications, your operation may be suffering from improper staffing at critical times and other inefficiencies. Delays and disruptions can occur randomly and rapidly, throwing your organization off its “regular” schedule. Using advanced shipping notifications within purchase orders and inventory management functions can help your business properly plan for labor needs. Having advance notice can help you to make sure that your operation has the time and workforce available when needed so that you can meet service requirements and keep costs down.Inventory Management Tips for an Optimized Warehouse
Inventory Management Tips: Optimizing Your Warehouse
Warehouse Tips Continued: Optimize Your Warehouse with these Inventory Management Tips
Inventory Management Continued: Tricks to Optimize Your Warehouse Operations
Inventory Management Tips Continued: Improving Warehouse Productivity
Inventory Management Continued: 5 Tips You Need to Know
Inventory Management Tips Continued: 5 Optimization Control Techniques for Warehouse Inventory