About Merchandise Warehouse Company
In operation for over 60 years, Merchandise Warehouse Company operates a 400,000 square foot multi-temperature warehouse strategically located in Indianapolis Indiana and includes inside rail. A second warehouse is under construction.
Experienced in providing first class warehousing services for the food, grocery, pharmaceutical and general commodity industries, Merchandise Warehouse Company (MWC) relies on leading edge technology to ensure the proper handling and storage of inventory. By using CCTV, EDI, WMS, radio frequency mobile computers and scanners, MWC is able to ensure optimal handling and warehouse services. A web portal enables MWC customers to have real time online access to activity reports, temperatures, climate monitoring and vital information about inventory.
MWC provides a wide array of value added services including blast freezing, tempering, inspection, labeling, temperature monitoring, kitting and assembly, import/export and packaging.
The Challenge
Warehouse Management Software Requirements
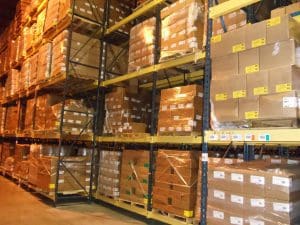

MWC was seeking new warehouse software in order to resolve communication issues, eliminate redundancy in paperwork and provide the flexibility needed to meet customer requirements. In addition, there was a need for real time information, greater accuracy and optimization of labor resources. In evaluating warehouse management software, MWC wanted leading edge technology that would:
- Provide the seamless flow of real time data visibility across its entire operation
- Enable systematic quality assurance control with comprehensive traceability including inspections and holds
- Automate billing and enable the use of any kind of billing scenario to ensure customer needs are met
- Enable reporting via subscriptions and emails rather than relying on human intervention for increased reliability
- Help improve operational efficiency and labor productivity
- Enable use of multiple mobile computing devices including forklift, handhelds and others
- Enable cycle counting
- Enable the use of lot codes and serial numbers with traceability
- Include transload and crossdock functionality
- Enable temperature reading and recording
- Include the ability to track pallets and create pallet transactions
- Integrate with Sage software
- Include EDI services
Zebra Mobile Computing Device Requirements
In selecting new handheld mobile computers, MWC needed devices that were ruggedized and rated for cold storage environments. After considering various options, MWC purchased OMNII XT15 devices, developed with the highest level of ruggedness and functionality. With its optimized ergonomics and balanced construction, weighted for comfort and practicality, the OMNII XT15 device helps to ensure that mobile workers are as efficient and effective as possible.
The OMNII XT15 combines a single versatile computing platform with the adaptability for future change in use. Featuring a Microsoft Windows CE 6.0 or Windows Embedded Handheld 6.5 operating system, the OMNII XT15 works seamlessly with Datex Footprint® WMS to provide top notch functionality and real time data.
“The decision to go with the Zebra OMNII XT15 devices was a simple one” explained Scott Whiting, Vice President and General Manager of Merchandise Warehouse Company. “These devices have leading edge functionality for cold storage environments and include a great warranty. They are exactly what we needed.”
Investing in new Zebra hardware has helped MWC to increase the accuracy of their operations and improve its ability to provide real time information to its customers.
The Solution
Datex Footprint® WMS and Zebra Mobile Computing Devices
In selecting the award winning Microsoft-based warehouse management system, Datex Footprint® WMS, Merchandise Warehouse Company wanted a system that would enable them to compete and win a more diversified range of customers. The new Datex warehousing software was evaluated to be highly flexible, enabling MWC to customize operations, reporting, billing and more to suit its many different types of customers.
“We use the realtime dashboards in our breakroom so employees see how they are progressing towards their bonuses” – Scott Whiting
Using the workflow-based warehouse management system, MWC now can automate processes specifically developed for each customer. This helps to ensure greater accuracy and labor productivity.
Using Zebra OMNII XT15 mobile computing device helps MWC to accurately capture more billing events in real time. This has helped to reduce the labor associated with billing and associated paperwork as there are also less errors to find and correct.
Datex Footprint® WMS has been especially useful in helping MWC in dealing with catch weight, an issue common in the 3PL cold storage warehouse industry. Datex Footprint® WMS also includes special functionality for cold storage warehouses including temperature reading and recording, and the ability to restrict inventory to specific temperature zones.
Improved Picking Process Optimizes Labor and Staging Area Space
An optimized picking process enables MWC to allocate inventory for shipping using a predetermined set of criteria so that the product can be staged and prepared ahead of time or simply picked and loaded onto the truck. MWC wanted a way to be able to pick and prepare shipments well in advance of the arrival of the trucks and to be able to pick the license plates after the dock appointment had been assigned a dock door. This helps to maximize the space used in the staging area.
MWC also now uses a two-step putaway process. Datex workflow helps to increase the speed and agility of the putaway process when different types of equipment are used to locate inventory in the correct locations. This allows the system to maintain the putaway task to be completed by another user.
3PL Billing Enhancements
Using the new Datex WMS software has enabled MWC to onboard new customers faster so that revenue can be generated more quickly. Using a combination of RF, mobile computing handheld devices and Datex software has enabled MWC to be able to capture and bill for every value added service and type of agreement.
Pallet Management
Datex Footprint® WMS includes a variety of tools to make pallet management easy and less time consuming. Every pallet is traceable, from the time it arrives until the time it leaves and is time stamped and sorted by the task completed. Datex WMS software reports pallets as unavailable during picking and reallocates to a new pallet without having to come to the dock office. The WMS can create pallet transactions and produce reports to aid in pallet management.
The Results
Labor, Time and Cost Savings
The adoption of the new workflow-based WMS and mobile technology has streamlined operations and created labor savings including the reduction of one Customer Service position. Operational processes have been optimized and automated to reduce errors and boost productivity. Using the new technology has resulted in cost savings on mailing out invoices and saves considerable time overall in “paperwork”.
Enhanced Customer Communications
In dealing with third party logistics customers, it is often the case that inventory and freight owners need continual communication and information about operations, inventory levels, orders and more. Using the new Datex-Zebra combined technology has enabled MWC to empower its clients to have real time access to information and reports however and whenever it is needed. The seamless flow of real time business intelligence has increased the already high level of customer satisfaction with MWC.
Increased Inventory Accuracy
As a result of the new Datex WMS software and Zebra mobile technology, Merchandise Warehouse Company realized an improvement in inventory from 98.6% to 99.9%.
Greater Access to Information through Customizable Reporting
Users now have access to a wide variety of reports in a user friendly interface that is simple to navigate. There is no longer a need to have users memorize shortcuts or commands due to the simplicity of the user interface. Having reports and data that is easy and fast to access has helped to increase the accuracy of MWC operations. Issues such as inactive inventory, production data and other matters can be quickly researched, evaluated and resolved.
User Friendly Technology Aids Helps System Adoption
MWC workers like the familiar user interface and more intuitive nature of the Datex WMS software. In addition, the fact that the Footprint® Help function is integrated into the system makes it easy for workers to find answers to questions. The system utilizes pictures and videos for every task in the software and also includes written instructions. Having a system includes an effective Help system aids in keeping workers productive and makes it easier when turnover occurs.
Advancement Towards a Paperless Operation
MWC identified that moving towards paperless operations would have significant value for its business. Eliminating manual operations and workarounds, written forms and printed bills has helped to not only make their business more “green”, but also has alleviated time wasted in finding and correcting errors, dealing with handwriting errors, processing paper invoices, mailings etc. and much more. Datex Footprint® WMS enables users to store any type of file including images, videos, documents, certificates etc. within the system for fast, easy access. Documentation can be attached to inbound and outbound shipments for easier research and accessibility. Information and documents can also be sent via email or shared on the web portal, making it easy for customers to access 24/7.
Value of Using Datex as a Turnkey Technology Solution Provider
To simplify its implementation, MWC selected Datex to provide the supply chain software, services and mobile computing hardware. “One vendor for a total technology solution eliminated the ‘finger pointing’ that can sometimes happen when too many companies get involved in a project. With Datex, with just one call we can get what we need” said Whiting.
Datex acts as an end-to-end technology solution provider and can provide supply chain software, mobile computing hardware, mobile device management, EDI and other professional services to help streamline and expedite implementation.
Recap:
In searching for a warehouse management system to improve the accuracy, productivity and visibility of their operation, Merchandise Warehouse Company selected Datex Footprint® WMS. Acting as the total solution provider, Datex provided the supply chain software, professional services, integrations and Zebra mobile computing hardware. Since the implementation of this integrated technology solution, MWC has recognized cost and labor savings, greater accuracy in inventory and operations and improved information visibility.
For more information on Merchandise Warehouse Co., visit them on the web at: www.mwindy.com